When it comes to teaching and learning at Universiti Kuala Lumpur (UniKL), the technical university has always been known for the hands-on and experiential learning elements in its programmes.
This initiative is further strengthened through its Pasir Gudang, Johor-based campus, UniKL Malaysian Institute of Industrial Technology (UniKL MITEC) which has developed a new simulator, Simulated Integrated Downstream Plant, that will begin operations in the middle of this year.
According to the Lecturer and Head of Section, Plant Engineering Technology (PEtech) at UniKL MITEC, Mohamad Shahrul Effendy Kosnan, the facility will expose students to crude oil processing methods involving instrumentation – including sensors as well as Fire and Gas System (FGS), as used by industry.
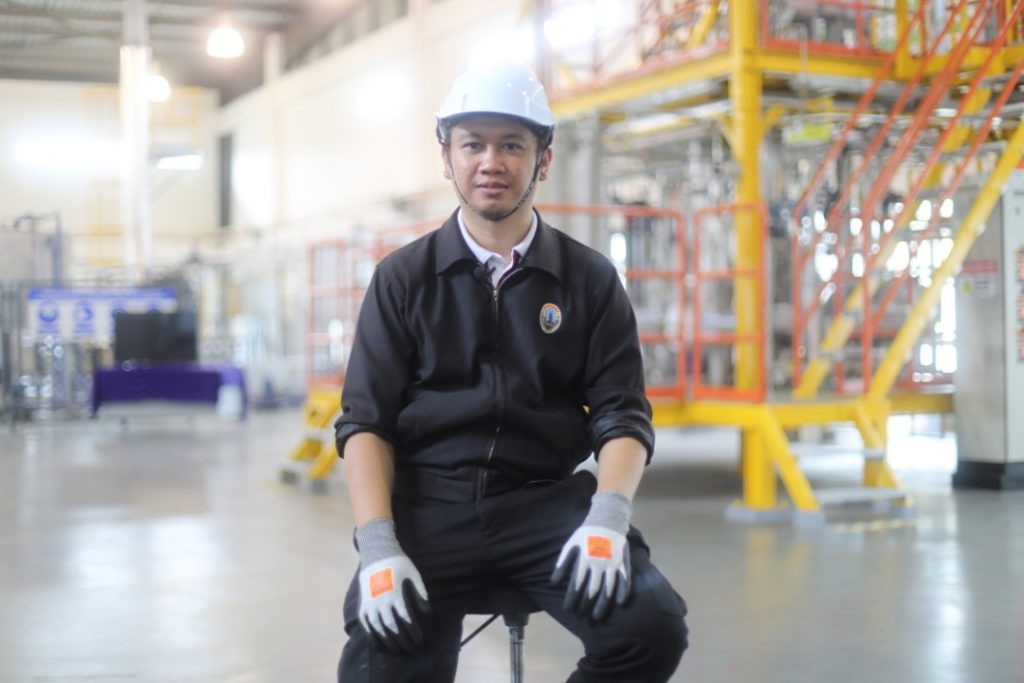
For the record, the safety, fire and gas leak detection systems are one of the main contents in the learning syllabus at UniKL MITEC.
“This simulated plant combines three units namely Mini Steam Power Plant, Crude Distillation Unit (CDU) and Hydrotreater Unit (HTU).
“Despite it being merely a simulator, it operates on a real-time basis because the Steam Power Plant is an actual facility used in the refining oil and gas sector.
“Currently, Mini Steam Power Plant Unit and the CDU are fully operational, while, HTU is expected to be handed over by the middle of this year,” said him.
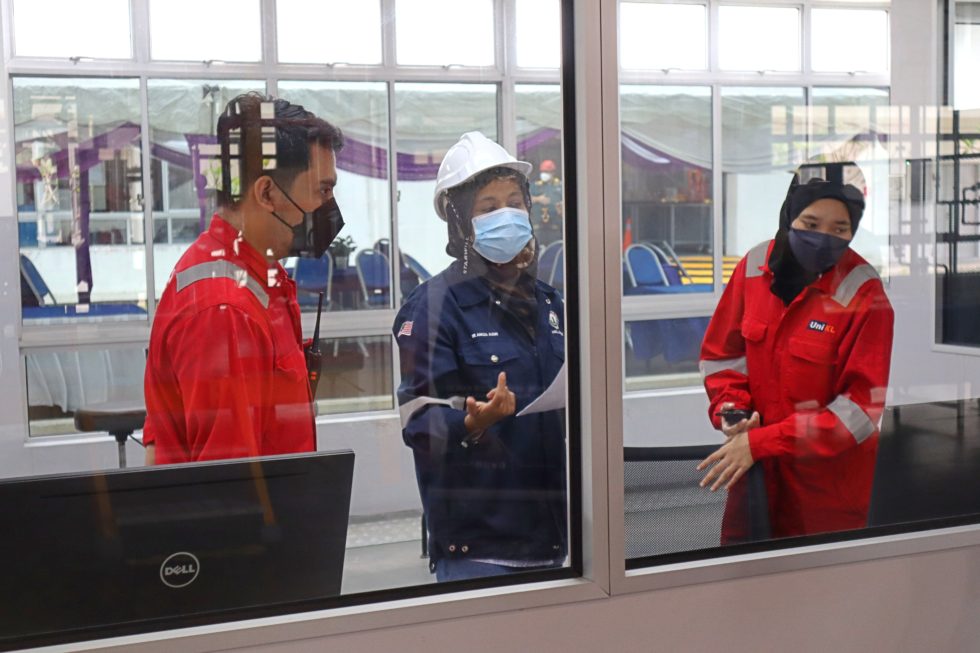
The stimulated plant – an initiative under the 10th and 11th Malaysia Plan, can be utilised for learning and teaching purposes through four courses offered at the campus that are Bachelor of Engineering Technology (Quality Engineering) with Honours; Bachelor of Engineering Technology (Hons) in Instrumentation and Control Engineering; Bachelor of Engineering Technology (Hons) in Facilities Maintenance Engineering and Bachelor of Petroleum Engineering Technology (Operation and Safety) with Honours.
This facility can be controlled manually and through the Remote Distributed Control System (DCS) which is operated in the main control room.
As emphasised by Mohamad Shahrul Effendy, the plant is capable of operating as a real operation in the petroleum refining industry where the facility can separate two mixed liquids such as ethylene glycol and water through CDU and also separate mixed liquids and gases such as ethylene glycol and nitrogen gas through the HTU.
Having this facility will help to train more skilled personnel in the field of operations, maintenance, and safety for the oil and gas industry.